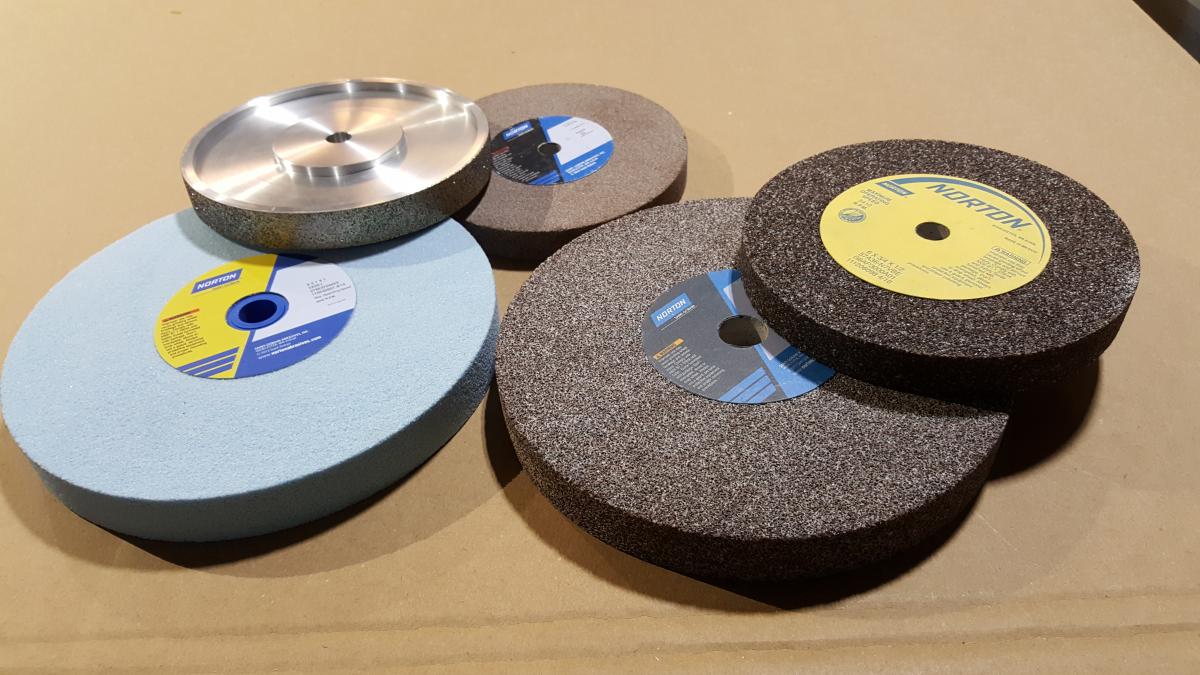
This is part 3 of a series on grinding:
Part 1: Introduction + When To Grind.
Part 2: The Technology of Grinding, Grinders, and Grinding Wheels.
Part 3: Grinding Wheel Chemistry and Nomenclature.
Part 4: Dressing Your Grinding Wheel for Cool Running.
Part 5: Grinding the Hollow.
Part 6: Repairing a Damaged Edge Without Burning the Steel.
Up until the late 19th century, grinding wheels were made of natural rock. Sheffield, England - that great center of edge tool manufacture - became the center it did because it had a lot of water power and, right outside the city, mountains of sandstone perfect for making grindstones. To this day, in the mountains of Derbyshire around Sheffield you can see remnants of grinding wheels everywhere. The problem with natural stones is that they are rarely consistent. If you are lucky, the inconsistency is just a hard or soft spot in the stone. If you are unlucky, a hidden flaw could cause the stone to explode. Another problem with natural stones: their grit is whatever their grit is, regardless of your expectations or needs.
In the late 19th century, Norton, an American company, figured out how to make a vitrified stone. The basic concept is simple. You take abrasive powder and mix it with a binder. Then you press it into a wheel shape and bake it in an oven. By varying the grit and binder you can make wheels with all sorts of properties.
To alter the abrasive aspect of the stone, you can vary the grit size. Coarser grits grind cooler but rougher. The space between the larger grits have more air and turbulence and keep the grit cooler. You can also use different abrasive materials for different purposes. Silicon Carbide grinds quickly but shatters under pressure, so your wheel will grind very fast for a short mount of time, then heat up as it rubs more than cuts. Aluminum Oxide crystals fracture slowly and therefore run much cooler - at a slightly slower grinding speed. Newer materials such as "seeded gel" are designed to fracture slowly along a crystal structure so that they still cut fast, but also run cool. Our 3X wheels are a consumer version of seeded gel and are the coolest running vitrified grinding wheels available.
Vitrified wheels can also have variable "friability." Friability means how much force it takes for the abrasive to detach from the wheel. A very friable wheel will constantly be losing particles as you grind. This is very messy, but each time you lose a grain of abrasive you also lose the heat on the grain. More importantly, this particle loss exposes fresh, sharp abrasive.
Finally, just recently, CBN plated wheels have come on the market. These wheels are a totally different technology and need to be looked at separately.
Lower grits run cooler; softer wheels run cooler; Seeded Gel (3X) runs cooler than Aluminum Oxide (AO); and everything runs cooler than Silicon Carbide.
To keep a wheel sharp and cutting cool and fast, you will need to regularly dress the wheel. This is a very critical step. More (lots more) on this later.
If you look at the side of a vitrified wheel, you will see a coding showing the material the wheel is made of, the grit, and a letter indicating hardness. If you are sharpening High Speed Steel (HSS) turning tools, which are very resistant to overheating, you can be less worried about heat than about surface finish. For regular carbon steel, heat avoidance is an important issue.
With a light touch, a properly dressed wheel, and a coarse enough grit, you can grind just about anything without overheating. But softer wheels with cooler abrasives make the job much easier.
For regular grinding of edge tools, I prefer a 3X wheel in either 46 or 60 grit. The slightly finer texture is a personal preference. For aluminum oxide wheels, I would want something even coarser - maybe 36 grit? Because I'm not a woodturner, a softer, more friable wheel ("I" Grade) is my preference. If you are using a 3X wheel also for grinding turning tools, you might want a "K" grade wheel. The stock wheels that come with most grinders are typically very coarse and very hard. While you can make them work for grinding edge tools, this option is far from optimal.
Dressing
None of these wheels will work properly unless they are regularly dressed. Dressing consists of rubbing a very hard stone or a row of diamonds against the rotating grinding wheel. This encounter rips off the top layer of the stone and exposes fresh, clean, SHARP grit. Sharp grit cuts faster and cooler. One way to make a hard grinding wheel run cooler is to dress is regularly. We also dress wheels to get any eccentricity out of them when we first mount them and when we want to curve the surface to make grinding easier. More on the technique of dressing later.
The typical wheel dresser is a block of rough diamonds in a block at the end of a stick. What you need to know is that single point diamond dressers are used in tool post grinders for precisely shaping a grinding wheel. We are hand holding our dresser, so a multipoint dresser is far more effective.
Our final choice is plated wheels. The newest grinding technology uses CBN (Cubic Boron Nitride) abrasive, a synthetic, diamond-like material that is plated onto an aluminum substrate wheel. Diamonds, being carbon-based, have a serious issue when grinding tool steel. The carbon on the tools and diamonds want to bond, and - even worse - diamonds are heat insulators, so like vitrified wheels, they reflect heat back into the tool. CBN, on the other hand, absorbs heat and the aluminum wheel just soaks up more heat. So the single coolest way of grinding these days is on a CBN wheel. And the bonus that you do not have to dress the wheels. The only caveat is that non-ferrous metals will clog the CBN wheel so if you mount a CBN wheel on your grinder, keep one side for a traditional wheel so that you can grind other stuff besides tool edges.
My current favorite grinding wheel is a 60 or 80 grit, crowned CBN wheel. The crowning which I will talk about next time is an important step for dressing and since you don't have to dress a CBN wheel. my CBN wheels have the crown built in. The downside of CBN is that it is more than twice as expensive as my next choice - a 3X wheel. But I really like the lack of maintenance and with no wheel dust flying off every time you dress the wheel I like the less mess.
I forgot to include a picture of a wheel dresser. I'll make up next time in part 4 when we mount our wheel on a grinder and dress it.
|
( CBN stands for cubic boron nitride, not nitrite )
Very much so. My grinder is a 3600rpm with a 80 grit CBN wheel on it. I barely need to quench a iron when grinding.